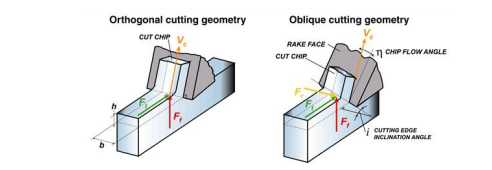
Orthogonal cutting also referred to as 2D cutting is a type of metal cutting in which the cutting tool approaches the workpiece with its cutting edge parallel to the uncut surface and at right angles to the direction of cutting. Thus, tool approach angle and cutting edge inclination are zero.
In orthogonal cutting, only two components of force are considered; the cutting force and the cutting force which can be represented by 2D coordinate system
Oblique Cutting also referred to as 3D cutting, is a type of cutting in which the cutting edge of the wedge shaped cutting tool makes an angle, except the right angle to the direction of tool motion.
In oblique cutting, three components of force are considered, that is thrust force, radial force and cutting force. These components cannot be represented by 2D coordinate system; they can only be represented by 3D coordinate system.
Key Difference
- In orthogonal cutting, the cutting edge of the tool makes right angle to the direction of feed motion whereas in oblique cutting, the cutting edge of the tool is inclined to the direction of feed motion.
- In orthogonal cutting, there are only two components of force which are mutually perpendicular. The components include: cutting force and thrust force ; On the contrary, in oblique cutting, three components of force are considered, that is thrust force, radial force and cutting force.
- The tool that uses orthogonal type of cutting has a lesser cutting life compared to tools that use oblique cutting.
- Orthogonal cutting has a high heat concentration at the cutting region when compared to oblique cutting which has a lesser concentration of heat at the cutting region.
- In orthogonal type of cutting, the cutting edge is larger than the cutting width whereas in oblique type of cutting, the cutting edge may or may not be larger than cutting width.
- In orthogonal cutting, the chips flow in the direction normal to the cutting edge whereas in oblique cutting, the chips flow along the sideways.
- In orthogonal type of cutting, the Shear force that act per unit area is high, a factor which increases the heat developed per unit area. On the other hand, the Shear force per unit is low; a factor which decreases heat developed per unit area hence increasing tool life.
- In orthogonal type of cutting, the surface finish obtained is very poor when compared to oblique cutting which gives a fairly good surface finish.
- Orthogonal type of cutting is used in grooving, parting, slotting, pipe cutting etc while oblique cutting is used almost in all industrial cutting, used in drilling, grinding, milling etc.
Also Read: Difference Between Shaper And Planer
Orthogonal (2D Cutting) Vs. Oblique-Cutting (3D Cutting) In Tabular Form
BASIS OF COMPARISON | ORTHOGONAL | OBLIQUE CUTTING |
Description | In orthogonal cutting, the cutting edge of the tool makes right angle to the direction of feed motion. | Oblique cutting, the cutting edge of the tool is inclined to the direction of feed motion. |
Components Of Force | There are only two components of force which are mutually perpendicular. The components include: cutting force and thrust force ; and can be represented by 2D coordinate system. | Three components of force are considered, that is thrust force, radial force and cutting force. These components cannot be represented by 2D coordinate system; they can only be represented by 3D coordinate system. |
Tool Life | The tool that uses orthogonal type of cutting has a lesser cutting life compared to tools that use oblique cutting. | The tool that uses oblique type of cutting has a more cutting life compared to tools that use oblique cutting. |
Heat Concentration At The Cutting Region | Has a high heat concentration at the cutting region. | Has a lesser concentration of heat at the cutting region. |
Cutting Edge | The cutting edge is larger than the cutting width. | The cutting edge may or may not be larger than cutting width. |
Chips Flow | The chips flow in the direction normal to the cutting edge. | The chips flow along the sideways. |
Shear Force Per Unit Area | The Shear force that act per unit area is high, a factor which increases the heat developed per unit area. | The Shear force per unit is low, a factor which decreases heat developed per unit area hence increasing tool life. |
Surface Finish | The surface finish obtained is very poor when compared to oblique cutting which gives a fairly good surface finish. | The surface finish obtained is a bit finer when compared to orthogonal cutting which gives a poor surface finish. |
Use | Used in grooving, parting, slotting, pipe cutting etc.. | Used almost in all industrial cutting, used in drilling, grinding, milling etc. |
Also Read: Difference Between Coining And Embossing Sheet Metal Operation
Comments are closed.