Many motion control applications use permanent magnet DC motors. Since it is easier to implement control systems using DC motors compared to AC motors, they are often used when speed, torque, or position needs to be controlled.
There are two types of commonly used DC motors: Brushed motors, and brushless motors (or BLDC motors). As their names imply, DC brushed motors have brushes, which are used to commutate the motor to cause it to spin. Brushless motors replace the mechanical commutation function with electronic control.
In many applications, either a brushed or brushless DC motor can be used. They function based on the same principles of attraction and repulsion between coils and permanent magnets. Both have advantages and disadvantages that may cause you to choose one over the other, depending on your application’s requirements.
What is Brushed motor?
A brushed DC electric motor is an internally commutated electric motor designed to be run from a direct current power source and utilizing an electric brush for contact.
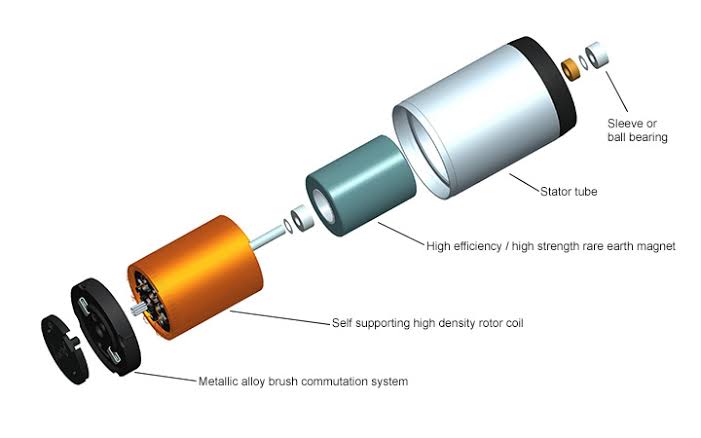
A brushed DC motor uses a configuration of wound wire coils, the armature, acting as a two-pole electromagnet. The current’s directionality is reversed twice per cycle by the commutator, a mechanical rotary switch. This facilitates flow of the current through the armature; thus, the electromagnet’s poles pull and push against the permanent magnets along the outside of the motor. The commutator then reverses the polarity of the armature’s electromagnet as its poles cross the permanent magnets’ poles.
Brushed DC motors can be varied in speed by changing the operating voltage or the strength of the magnetic field. Depending on the connections of the field to the power supply, the speed and torque characteristics of a brushed motor can be altered to provide steady speed or speed inversely proportional to the mechanical load.
Applications of Brushed DC motor
- Though these motors mainly use in household appliances and in automobiles.
- These motors still use for industrial purposes for both low and high power, fixed and variable speed electric drives.
- They still use for paper machines, cranes, electrical propulsion, sewing machines, power tools, and steel rolling mills.
What is a Brushless motor?
A brushless DC electric motor, also known as an electronically commutated motor or synchronous DC motor, is a synchronous motor using a direct current electric power supply. It uses an electronic closed loop controller to switch DC currents to the motor windings producing magnetic fields which effectively rotate in space and which the permanent magnet rotor follows. BLDC motors are superior to brushed DC motors in many ways, such as ability to operate at high speeds, high efficiency, and better heat dissipation.
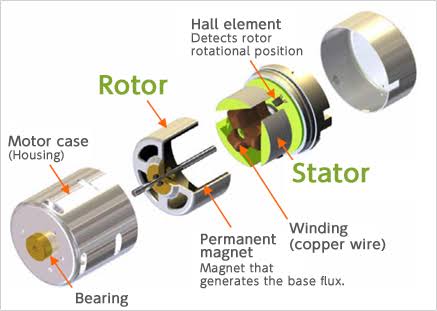
They are an indispensable part of modern drive technology, most commonly employed for actuating drives, machine tools, electric propulsion, robotics, computer peripherals and also for electrical power generation. With the development of sensorless technology besides digital control, these motors become so effective in terms of total system cost, size and reliability.
Application of Brushless motors
Applications that use the BLDC Motor include, yet are not constrained to:
- Consumer electronics
- Transport
- Heating and ventilation
- Industrial engineering
- Model engineering
Also Read: Difference Between 2 Pole And 4 Pole Motor
Brushed vs Brushless motors
BASIS OF COMPARISON | BRUSHED MOTOR | BRUSHLESS |
Description | A brushed DC electric motor is an internally commutated electric motor designed to be run from a direct current power source. | A brushless motor is a direct current (DC) electric motor that operates without the mechanical brushes and commutator of a traditional brush motor. |
Delivery of Current | Brushed DC motors use brushes to deliver current to the motor windings through mechanical commutation | Brushless motors use Electrical commutation to deliver the current. |
Speed | Speed range in brush motors is lower than brushed types. | Speed range in brushless motors is higher than brushed types due to the absence of brushes and commutators. |
Noise | They are best suited for extreme noisy environment such as in industries to compensate for cost investment. | They are best suited for smooth and noiseless application. |
Speed Control | Brushed motors require more complicated methods of speed control. | Brushless motors offer higher speed controllability compared to the brushed types. |
Efficiency | Due to power losses through friction and power transfer via its commutator system, brushed motors are relatively inefficient. | Brushless motors, are more efficient due to the lack of mechanical losses seen in brushed motors. |
Lifespan | Brushed motors have shorter lifespans, due to the wear and tear of the brushes. | Owing to their design, brushless motors have longer lifespans. |
Application | Brushed motors are used in home appliances, kid toys, industrial applications, medical equipment, robots, and drones to electric cars, power tools, etc. | Brushless motors are used in electric vehicles, hybrid vehicles, and electric bicycles, industrial applications, drones, washing machines, fans, pumps, and blowers, etc. |
Input Switch | The input is switched using mechanical commutations through slip ring commentators. | The input is switches using electronic commutations though semiconductor switches. |
Cost | The overall cost is cheaper than brushless motor. | Brushless motors are quite expensive. |
Overheating | The continuous sliding of brushes with the commutator generates heat. | There is no overheating problem due to friction. |
Rotor | The rotor contains armature winding. | The rotor is made of permanent magnet. |
Design | It has very simple design and construction including only a single winding. | The motor design is complex where the stator contains multiple separate windings. |
What you needto know about Brushless motors
- Brushless motors are permanent magnet motors that produce motion by pushing or pulling on something with a spinning rotor.
- Brushless motors produce less noise than brushed motors, and they require no maintenance because there are no brushes or commutators needed like in brushed motors.
- Brushless motors are more expensive than brushed motors.
- Brushless motors are Higher efficiency than brushed motors.
- Brushless motors are a Longer motor life than brushed motors.
- Brushless motors are Faster control response and speed.
- Brushless motors can run at higher speeds for longer periods.
- Brushless motors require more power than brushed motors to spin the rotor, but brushless motors offer benefits such as less noise and vibration which makes them very popular in high-performance electric vehicles such as model racing cars.
- Brushless motors don’t need to be lubricated, which is good because they tend to be more sensitive to dust and contamination than brushed motors.
- Brushless motors are often used in computers running robotic servomechanisms, 3D printers, CNC machines, electric bikes, and cars mostly because of their high torque capabilities.
- Brushless motors are typically found in electric vehicles. meaning that they produce on-demand more power while using less battery or having a longer lifespan on the same amount of charge.
What you need to know about Brushed motors
- Brushed motors are the most common type of DC motor. They have a spinning armature with copper coils that interact with magnets to create rotational force. The commutator on the spinning armature continually switches the current flowing through the coils so that it flows in the correct direction. This ensures that the rotor (armature) continues spinning in the correct direction.
- Brushed motors are generally low-cost and reliable when a constant speed is required, but they require regular maintenance to ensure long-term reliability. The brushes provide two main functions:
- To collect electric current from stationary wire commutators on the rotating armature. and to change the direction of the current to spin the armature in the correct direction.
- A brushed motor uses brushes to change the direction of current flow, whereas a brushless motor doesn’t need brushes as it has a Hall effect sensor to detect the position of the rotor.
- Brushed motors are generally low-cost and reliable when a constant speed is required.
- A brushed motor uses brushes to change the direction of current flow, whereas a brushless motor doesn’t need brushes as it has a Hall effect sensor to detect the position of the rotor.
- Brushed motors are high in friction losses and greater power consumption compared to a brushless motor where the circumference is smaller at only one end of the armature.
- Brushed motors generate less wasted power when operating at lower speeds (e.g., when starting from rest).
Also Read: Difference Between Servo motor And Stepper Motor