Job order costing or job costing is a system for assigning and accumulating manufacturing costs of an individual unit of output. The job order costing system requires a separate job cost record which reports each item’s direct materials and director labor that were used and assigned amount of manufacturing overhead. The record may also show work-in-progress inventory and the finished goods inventory.
Process costing is used when there is mass production of similar products, where the costs associated with individual units of output cannot be differentiated from each other. Process costing is used in industries such as oil refining, food production and chemical processing. Below, find more insights on differences between job order costing and process costing.
Key Differences
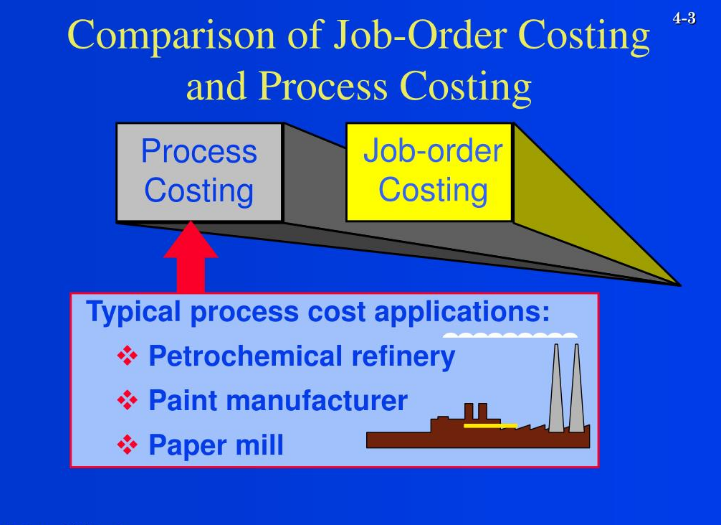
Description
Job order costing or job order costing is a system for assigning and accumulating manufacturing costs of an individual output. This system of costing is used when the various items produced are different from each other and each has a significant cost. Process costing on the other hand, is a system of costing that involves collecting and assigning manufacturing costs to the units produced.
Work-in-Progress (WIP)
In job order costing, the probability of work-in-progress arising is very small and if it arises it is for a specific job and not for the entire production line. Process costing on the other hand, records work-in-progress because when production begins, produced goods have to be transferred between different departments and therefore these goods have to be treated as work-in-progress.
Maintenance of Job Cost Sheets
In job order costing, a Job Cost Sheet is maintained based on individual job cards and time clocks. This basically shows the exact time an employee has spent on an individual job, so that the labor cost could be attributed directly to these jobs. Conversely, in process costing no job cost sheets are maintained because production focus in this technique of costing relies upon the output of departments.
Calculation
In job order costing, the cost is calculated for each job; this means that for every job completed by a factory, direct cost (labor and material) can be attributable to each individual job. However in Process Costing the first thing is that all the costs of each process are calculated and then divided over the number of units produced.
Suitability
Job order costing is suitable for industries where orders need to be completed for an individual customer such as investment companies, hospitals, firms or fashion industry. In these companies, an individual customer represents a single job and each job needs to be carved for each individual customer. On the contrary, process costing is suitable for the industries that need to produce large volumes of homogeneous products e.g pen manufacturers, brick manufacturers, packagers and process food manufacturers.
Cost Transfer
In job costing, the costs are determined exclusively for each job and therefore no transfer of costs is required. While in process costing, costing costs need to be transferred from one process to another.
Possibility of Cost Reduction
The possibility of cost reduction is very less in job order costing whereas in process costing, the possibility of cost reduction is comparatively high.
Determination of Costs
In job order costing, the costs are determined after the completion of the job, but in process costing, the cost of each job is already determined.
Application
The job order costing is used for the costing of products that are more unique and customizable. This applies to products that are produced in small volumes, whereas, process costing is used for the costing of more standardized products that are usually produced in large volumes.
Record Keeping
A lot of record keeping is required for job costing since time and material must be charged to specific jobs. Process costing on the other hand, aggregates costs and so requires less record keeping.
Difference between Job order costing and Process Costing In Tabular Form
Points of Comparison | Job order costing | Process Costing |
Definition | Job order costing or job order costing is a system for assigning and accumulating manufacturing costs of an individual output. | Process costing is a system of costing that involves collecting and assigning manufacturing costs to the units produced. |
Work-in-Progress (WIP) | When using this system of cost accounting, the probability of work-in-progress arising is very small and if it arises it is for a specific job and not for the entire production line. | It records work-in-progress because when production begins, produced goods have to be transferred between different departments and therefore these goods have to be treated as work-in-progress. |
Maintenance of Job Work Sheet | In this system of costing, a Job Cost Sheet is maintained based on individual job cards and time clocks. This basically shows the exact time an employee has spent on an individual job, so that the labor cost could be attributed directly to these jobs. | No job cost sheets are maintained because production focus in this technique of costing relies upon the output of departments. |
Calculation | In this method, the cost is calculated for each job; this means that for every job completed by a factory, direct cost (labor and material) can be attributable to each individual job. | In this method, the first thing is that all the cost of each process is calculated and then divided over the number of units produced. |
Suitability | It is suitable for industries where orders need to be completed for an individual customer such as investment companies, hospitals, firms or fashion industry. In these companies, an individual customer represents a single job and each job needs to be carved for each individual customer. | It is suitable for the industries that need to produce large volumes of homogeneous products e.g pen manufacturers, brick manufacturers, packagers and process food manufacturers. |
Cost Transfer | The costs are determined exclusively for each job and therefore no transfer of costs is required. | Costing costs need to be transferred from one process to another. |
Possibility of Cost Reduction | The possibility of cost reduction is very less in job order costing. | In process costing, the possibility of cost reduction is comparatively high. |
Determination of Cost | In this system of costing, the costs are determined after the completion of the job. | In this system of costing, the cost of each job is already determined. |
Application | It is used for the costing of products that are more unique and customizable. This applies to products that are produced in small volumes. | It is used for the costing of more standardized products that are usually produced in large volumes. |
Record Keeping | A lot of record keeping is required for job costing since time and material must be charged to specific jobs. | Process costing aggregates costs and therefore requires less record keeping. |
5 Similarities between Job costing and Process costing
- Both job order costing and process costing systems have the same goal which is allocation of expenses like labor, material, production and nonproduction overheads to the end products in the manufacturing process.
- Both job order and process costing have the same cost flows and thus inventory accounts used for recording accounting entries are almost the same. Example of accounts used is material, work-in-progress etc.
- Job order costing uses the same method of assigning overheads to the individual jobs that process costing uses to assign to a whole production process.
- Manufacturing accounts (T-accounts) are maintained in both job order costing and process costing.
- Information and data collected from both processes (job order costing and Process costing) is used by the management of the business for decision making purposes.
Summary
What is the main difference between Job order costing and Process costing?
Job order costing or job order costing is a system for assigning and accumulating manufacturing costs of an individual output. This system of costing is used when the various items produced are different from each other and each has a significant cost. On the other hand, Process costing is used when there is mass production of similar products, where the costs associated with individual units of output cannot be differentiated from each other.