What Is MIG (Metal Inert Gas) Welding?
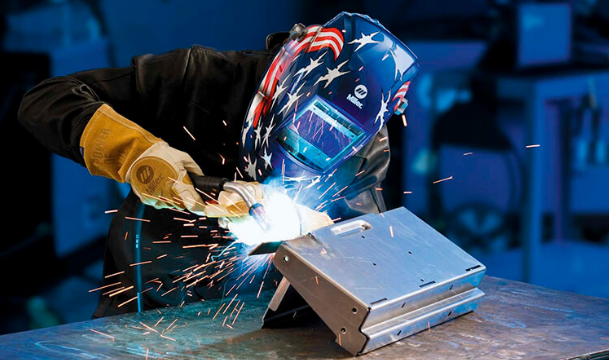
Metal Inert Gas (MIG) welding is a welding process in which an electric arc forms between a consumable MIG wire electrode and the workpiece metal, which heats the workpiece metal, causing them to melt and join. The wire electrode is wrapped in a wire-pool and is continuously fed to the welding zone with help of an automatic arrangement. A shielding gas is also supplied in the welding zone from a separate gas cylinder in order to protect the hot weld from oxidation and contamination.
In addition to general shielding of the arc and the weld pool, the shielding gas performs a number of important functions:
- Forms the arc plasma
- Stabilizes the arc roots on the material surface
- Ensures smooth transfer of molten droplets from the wire to the weld pool.
MIG welding is very effective and efficient when in manufacturing automobiles and building process of bridges. MIG is also used in fabrication of sheet metal and it can also be used for deep groove welding.
What You Need To Know About Metal Inert Gas Arc Welding (MIG)
- MIG is a welding process in which electric an arc electric arc is formed between a consumable wire electrode and workpiece metal.
- Metal inert gas (MIG) welding utilizes a consumable electrode that is continuously fed into the welding zone from a wire pool.
- The equipment used in TIG welding process is welding torch, non-consumable tungsten electrode, a constant-current welding power supply and a shielding gas source.
- MIG is simple and usually does not require highly trained welder. It is also very easy to control.
- MIG welding is commonly carried out either in AC or in DCEP polarity so that electrode can be melted and deposited at a faster rate.
- The utilized gas in MIG is a mixture of carbon dioxide and argon.
- Composition of electrode metal is selected based on parent metal. Usually, metallurgical composition of electrode metal is similar to that of base metal.
- MIG does not result to tungsten inclusion defect.
- MIG is particularly suitable for homogenous welding. It cannot be carried out in autogenous mode welding as filler is applied inherently.
- MIG can be used to weld materials such as mild steel, stainless steel and aluminum. Also TIG can weld a wider range of material thickness i.e from heavy structural plates to thin gauge sheet metal.
- Filler decomposition rate is very high. Therefore, the process is highly productive.
- MIG cannot work in any position.
- In MIG, the appearance and quality of weld bead is not very nice.
- MIG welding usually produce spatter. This normally results to loss of costly filler metal.
- MIG welding filler typically comes in the form of a small diameter (0.5- 2 mm) and very long (several hundred meters) wire that wound in a wire-pool.
- Due to very large length, the filler electrode can be fed for a longer duration without replacement.
- It is a faster welding process.
- It uses a continuous wire feed.
- In MIG, no filler metal is required. The feed electrode wire melts and acts as filler metal.
- MIG uses constant voltage, direct current power source for the welding. It can also use constant current system and alternating current.
What Is Tungsten Inert Gas Arc (TIG)Welding?
Tungsten Inert Gas (TIG) welding also referred to as Gas Tungsten Arc Welding (TIG) is an arc welding process that uses a non-consumable tungsten electrode to produce the weld. In TIG filler is normally used and the welding zone and electrode has to be protected from atmospheric oxidation and contamination by an inert shielding gas (either argon or helium).
Unlike MIG welding where the electrode material is selected based on the composition of base metal, TIG welding utilizes a tungsten electrode irrespective of the chemical composition of the base metals. TIG is mostly used to weld thin sections of stainless steel and non-ferrous metals such as aluminum, magnesium and copper alloys. If done properly, TIG welding can produce a defect-free sound joint with very good appearance.
What You Need To Know About Tungsten Inert Gas Arc Welding (TIG)
- TIG is a process in which an electric arc is formed in between a non-consumable tungsten electrode and workpiece metal.
- Tungsten inert gas (TIG) welding utilizes a non-consumable electrode and therefore it remains static and intact during welding.
- The equipment used in TIG welding process is welding torch, non-consumable tungsten electrode, a constant-current welding power supply and a shielding gas source.
- TIG is somehow difficult especially in establishing and maintaining the arc. It requires a skilled welder.
- TIG welding is commonly carried out either in AC or DCEN polarity to increase electrode life.
- In TIG, argon is the only utilized gas.
- In TIG welding, electrode is always made of tungsten with small proportion of other alloying elements like thorium.
- TIG welding sometimes results to tungsten inclusion defect. Tungsten inclusion defect occur when a melted/broken part of the tungsten electrode gets embedded into weld bead.
- TIG is specifically suitable for autogenous mode welding. It can also be employed for homogenous or heterogeneous mode by supplying additional filler.
- TIG is used to weld materials like kitchen sinks and tool boxes. Pipe welding and other heavy tasks can also be performed. In this case, what is only required is a unit with ability to put out the amount of power needed.
- In TIG, filler decomposition rate is comparatively low. Therefore, the process is not very productive.
- TIG can be worked in any position.
- TIG can easily produce defect-free reliable joint with good appearance.
- TIG welding is mostly free from spatter.
- TIG welding filler generally comes in the form of small diameter (1-3 mm) and short length (60-180 mm) rod.
- Due to short length, frequent replacement of the filler is required. This usually interrupts the welding process unintentionally.
- It is a slower welding process.
- It does not use a continuous wire feed.
- TIG may require filler metal from outside in some cases if needed.
- TIG uses constant current welding power supply for the welding.
Also Read: Difference Between AC And DC Welding
Between MIG And TIG Welding In Tabular Form
BASIS OF COMPARISON | TIG Welding | MIG Welding |
Description | TIG is a process in which an electric arc is formed in between a non-consumable tungsten electrode and workpiece metal. | MIG is a welding process in which electric an arc electric arc is formed between a consumable wire electrode and workpiece metal. |
Electrodes Used | It utilizes a non-consumable electrode and therefore it remains static and intact during welding. | It utilizes a consumable electrode that is continuously fed into the welding zone from a wire pool. |
Equipment | The equipment used in TIG includes welding torch, non-consumable tungsten electrode, a constant-current welding power supply and a shielding gas source. | The equipment used in MIG include welding gun, a welding power supply, a feed wire unit, a welding electrode wire and a shielding gas supply. |
Skill Requirement | It is somehow difficult especially in establishing and maintaining the arc. It requires a skilled welder. | It is simple and usually does not require highly trained welder. It is also very easy to control. |
How It Is Carried Out | It is commonly carried out either in AC or DCEN polarity to increase electrode life. | It is commonly carried out either in AC or in DCEP polarity so that electrode can be melted and deposited at a faster rate. |
Utilized Gas | Argon is the only utilized gas. | The utilized gas in MIG is a mixture of carbon dioxide and argon. |
Composition Of Electrode | Electrode is always made of tungsten with small proportion of other alloying elements like thorium. | Composition of electrode metal is selected based on parent metal. Usually, metallurgical composition of electrode metal is similar to that of base metal. |
Tungsten Inclusion Defect | It sometimes results to tungsten inclusion defect. | It does not result to tungsten inclusion defect. |
Suitability | TIG is specifically suitable for autogenous mode welding. | MIG is particularly suitable for homogenous welding. |
Used To Weld | It is used to weld materials like kitchen sinks and tool boxes. | It can be used to weld materials such as mild steel, stainless steel and aluminum. |
Filler Decomposition Rate | Filler decomposition rate is comparatively low. | Filler decomposition rate is very high. |
Working Position | TIG can be worked in any position. | MIG cannot work in any position. |
Surface Finish | It can easily produce defect-free reliable joint with good appearance. | The appearance and quality of weld bead is not very nice. |
Spatter | Mostly free from spatter. | Usually produce spatter. |
Filler | TIG welding filler generally comes in the form of small diameter (1-3 mm) and short length (60-180 mm) rod. | MIG welding filler typically comes in the form of a small diameter (0.5- 2 mm) and very long (several hundred meters) wire that wound in a wire-pool. |
Filler Replacement | Frequent replacement of the filler is required. | The filler electrode can be fed for a longer duration without replacement. |
Nature Of The Process | It is a slower welding process. | It is a faster welding process. |
Continuous Wire Feed | It does not use a continuous wire feed. | It uses a continuous wire feed. |
Filler Requirement | May require filler metal from outside in some cases if needed. | No filler metal is required. |
Kind Of Power Used For Welding | Uses constant current welding power supply for the welding. | Uses constant voltage, direct current power source for the welding. |
Also Read: Difference Between Soldering, Welding And Brazing
Similarities Between MIG And TIG Welding?
- Both processes use bare electrode.
- In both processes, shielding gas is required to supply from additional sources.
- Only conductive metals can be joined by MIG and TIG.
- In both cases, inert shielding gas is used to protect hot weld bead from oxidation and contamination.
Comments are closed.