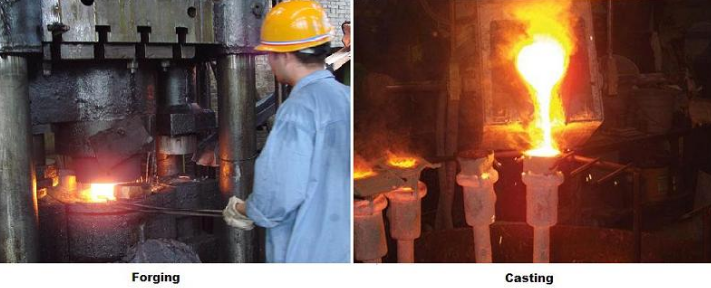
Forging
Forging is the metalworking process involving the shaping of metal using localized compressive forces. At the end of the forging process, the resulting product features extreme strength, impact toughness and wear resistance due to thermal and mechanical treatment. Forging can be classified according to the temperature at which it performed: cold forging, warm forging or hot forging.
- Warm Forging: the raw material is heated at temperatures between 800 and 1000 degrees Celsius.
- Hot forging: when the raw material is heated at temperatures above 1000 degrees Celsius.
- Cold forging: when the raw material is heated at room temperature.
Forging process is most appropriate for:
- Parts that can withstand strong impacts and mechanical force
- Parts that are highly resistant to wear and tear
- Parts are susceptible to stress and heavy loads
- Parts that generally require extremely high strength, toughness and resistance
Casting
Casting is the metalworking process involving pouring liquid metal into molds with cavity to obtain required shapes. The final product of casting may undergo surface finish treatment such as painting, powder coating, polishing and other forms of coating such as zinc plating. There are three different methods of casting which include: investment casting, sand casting and die casting.
- Investment casting also referred to as precision casting is the process whereby a wax pattern is coated with a refractory ceramic material. Then the wax is melted out and the molten metal is poured into the cavity where the wax pattern was.
- Sand casting also referred to as molded casting, is characterized by use of sand as mold material. Nearly all metal castings are produced through sand casting process.
- Die casting is characterized by forcing molten metal under high pressure into a mold cavity. The mold cavity is made using two hardened tool steel dies which have been machined into shape and work similarly to an injection mold during the process.
The casting process is most appropriate for:
- Large sized parts
- Parts requiring mass production
- Parts with internal cavities
- P arts in special alloys.
Also Read: Difference Between Cold Working And Cold Working Process
The Difference Between Forging And Casting In Tabular Form
Basis of Comparison | Forging | Casting |
Description | Forging is the metalworking process involving the shaping of metal using localized compressive forces. | Casting is the metalworking process involving pouring liquid metal into molds with cavity to obtain required shapes. |
Product Strength | Forged materials are stronger because they have a definite grain structure which is pressed with compressive force, increasing their mechanical strength. | Casted material is low in strength as they are poured into a cavity which eventually allows the material to take its shape. |
Uniformity | The forged material is usually made to a uniform structure preserving consistency in shape. | The casted material is not usually uniform. |
Finishing | Forging does not require a secondary finishing operation. | Casting requires a secondary finishing operation. |
Aim | Forging is aimed at producing uniform and simple material. | Casting is aimed at producing complex patterns and shapes. |
Types | Types of forging include: Warm forging Cold forging Hot forging | Types of Casting include: Die casting Investment casting Sand casting |
Preference | Forging is most preferred for materials that can withstand strong impact and mechanical force. | Casting is preferred for materials requiring mass production or materials that need to be produced with cavities (Hollow spaces). |
Material Restrictions | In forging, materials weighing more than 50Kgs will require higher power and in such case casting would be the most appropriate process. | Casting does not have material limitations, any size, weight or shape of material can be melted before molding them into required shape. |
Equipments | Equipments and machines used for forging such as duty industrial dies are highly expensive. | Equipments used in casting are relatively cheap when compared to those used in forging. |
Also Read: Difference Between Coining And Embossing Sheet Metal Operations
Application of Casting And Forging
Casting and forging is used to produced parts and equipments of the following industries:
- Petrochemical Plants
- Power generation plants
- Mining and mineral processing
- Brickworks
- Railways
- Aeronautical
- Automobile (pulleys and gear wheels)