The polarity of the electric current created by the welding machine, which runs through the electrode, is either AC or DC. These are the two types of polarity and the welding quality and efficiency depend significantly on the type of current used.
AC Welding
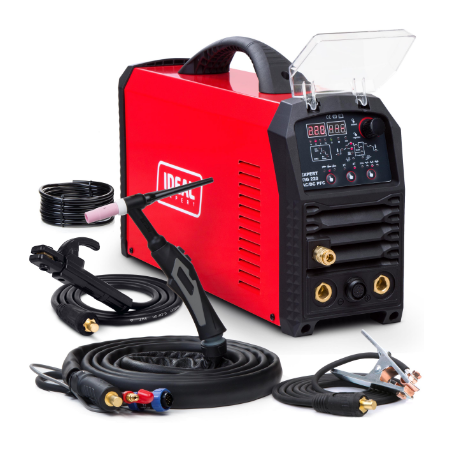
AC stands for Alternating Current. In an AC electric circuit, the atoms leaving the supply are swinging from being positively charged to being negatively charged. The poles keep changing back and forth from positive to negative and the flow changes direction. Using an AC welding power supply, the polarity of the arc is always changing (alternative) from positive to negative. The use of an AC welder with the flow alternating reduces “arc blow’’ and produces a better weld. AC welding is best suited for:
- Down-hand heavy plate welding
- Fast fill welding
- Aluminum TIG with high frequency.
What You Need To Know About AC Welding
- Arc welding with an AC power supply, the polarity of the arc is always changing (Alternating Current) from positive to negative and the flow must change direction.
- It is used in the welding of aluminum and other non-ferrous metals.
- AC is used for a few specific types of welding, that is, down-hand heavy plate, fast fill and aluminum TIG with high frequency.
- AC produces high amount of spatter, resulting in a rough weld and low product yield.
- AC is efficient only in welding thick and heavy metals and thus not preferable by many welders.
- Usually machines that require AC to function are very much expensive.
- The risk of arc blow in case a magnetic field builds up is greatly reduced in AC welding. Thus it can be used for magnetized metal welding.
- AC allows welding/ works perfectly under higher temperatures.
- The reliability of AC type of current is very low and thus difficult to work with.
- AC machines are somehow tedious to use and handle.
- The AC welding tends to be slower and results in slow electrode melt off.
- Achieves a deeper weld penetration.
DC Welding
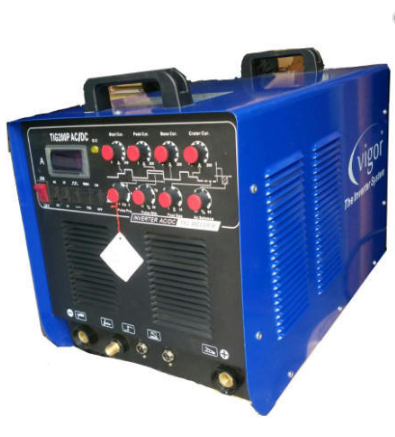
DC stands for Direct Current. In a DC electric circuit, there is a constant negative pole and a constant positive pole. The flow of electricity is created when negatively charged atoms, produced by the power supply are moving towards the positive pole to pair with the positively charged atoms. This eventually creates an electric flow from the negative pole towards the positive pole. In a DC current welding, the polarity to the base metal and electrode remains the same during welding unless the polarity is changed manually. Typically DC currents include the current in batteries and often used in low voltage devices such as cell phones and remote controls. DC welding is best suited for:
- Hard facing
- Overhead or vertical welding
- Build-up of heavy deposits
- Single carbon brazing
- Stainless steel TIG welding
What You Need To Know About DC Welding
- Arc welding with a DC power supply, the polarity of the electric arc is a constant flow in one direction from negative to positive.
- It is use in welding of ferrous metals.
- DC is used for a few specific types of welding like vertical welding, single carbon brazing, and stainless steel TIG welding etc.
- DC type of current produces a lower amount of spatter, resulting in a smooth weld and higher product yield.
- DC is most efficient in welding thinner metals and thus it is desirable to many welders.
- Usually machines that require DC to function are very much affordable.
- There is usually a high risk of arc blow if a magnetic field builds up.
- DC does not work well for high heat intensity.
- The reliability of DC type of current is higher, making it much easier to work with.
- DC welding tends to be faster and results in quicker electrode melt off.
- DC machines are easy to handle and use.
- Does not necessarily achieve a deeper weld penetration.
Also Read: Difference Between TIG And MIG Welding
Difference AC And DC welding in Tabular Form
BASIS OF COMPARISON | AC WELDING | DC WELDING |
Description | Arc welding with an AC power supply, the polarity of the arc is always changing (Alternating Current) from positive to negative and the flow must change direction. | Arc welding with a DC power supply, the polarity of the electric arc is a constant flow in one direction from negative to positive. |
Use | It is used in the welding of aluminum and other non-ferrous metals. | It is use in welding of ferrous metals. |
Application | AC is used for a few specific types of welding, that is, down-hand heavy plate, fast fill and aluminum TIG with high frequency. | DC is used for a few specific types of welding like vertical welding, single carbon brazing, and stainless steel TIG welding etc. |
Spatter | AC produces high amount of spatter, resulting in a rough weld and low product yield. | DC type of current produces a lower amount of spatter, resulting in a smooth weld and higher product yield. |
Efficiency | AC is efficient only in welding thick and heavy metals and thus not preferable by many welders. | DC is most efficient in welding thinner metals and thus it is desirable to many welders. |
Affordability | Usually machines that require AC to function are very much expensive. | Usually machines that require DC to function are very much affordable. |
Risk Of Arc Blow | The risk of arc blow in case a magnetic field builds up is greatly reduced in AC welding. Thus it can be used for magnetized metal welding. | There is usually a high risk of arc blow if a magnetic field builds up. |
Effect Of High Temperature | AC allows welding/ works perfectly under higher temperatures. | DC does not work well for high heat intensity. |
Reliability | The reliability of AC type of current is very low and thus difficult to work with. | The reliability of DC type of current is higher, making it much easier to work with. |
Work Efficiency | The AC welding tends to be slower and results in slow electrode melt off. | DC welding tends to be faster and results in quicker electrode melt off. |
Handling Of Machine | AC machines are somehow tedious to use and handle. | DC machines are easy to handle and use. |
Weld Penetration | Achieves a deeper weld penetration. | Does not necessarily achieve a deeper weld penetration. |
Also Read: Difference Between Soldering, Welding And Brazing