For any machinist, one among many of the basic concepts to understand in any milling process is the cut direction. Milling cutters can cut in two directions, conventional (sometimes known as up milling) or climb (sometimes known as down milling).
In conventional milling, milling cutter rotates against the direction of feed of workpiece, the chip thickness is zero at the entrance of cutting tooth and maximum at tooth exit. At the beginning of milling, the tool does not cut; it just slides across the surface of the material until sufficient pressure is built up.
In climb milling, the milling cutter rotates in the same direction of feed of workpiece, while the chip thickness is maximum at the entrance of cutting tooth and minimum at tooth exit. Each tooth engages the material at a definite point. Get more insights on how the two milling processes differ from one another.
Climb Milling Vs. Conventional Milling: The Differences
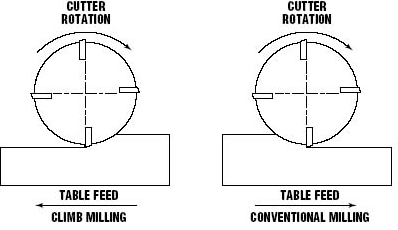
Chip thickness
In conventional milling, the chip width is zero at the entrance of cutting tooth and increases as the cutter finishes slicing, a factor which causes more heat to diffuse into the workpiece producing work hardening. Climb milling on the other hand, chip width is maximum at the entrance of cutting tooth and decreases at tooth exit, so heat generated will more likely transfer to the chip.
Milling Cutter Rotation
In conventional milling, milling cutter rotates against the direction of feed of workpiece whereas, in climb milling, milling cutter rotates in the same direction of feed of workpiece.
Cutting Force
In conventional milling, less tool deflection is encountered but more fixturing is needed (cutting force is directed away from the workpiece. Conversely, in climb milling more tool deflection is encountered but less fixturing needed (cutting force is directed onto the workpiece.
Cutting Process
The cutting process in conventional milling leaves chips ahead of the cutter. It is carried upward by the tool. Conversely, the cutting process in climb milling leaves chips behind the cutter. It is carried by the tool.
Surface Finish
Surface finish in conventional milling is poor when compared to climb milling. It is generally used for the rough surface cutting operation. Due to good surface finishing, climb milling is used for finishing operation.
Tendency
Conventional milling has no tendency to drag workpiece towards the cutter whereas; climb milling shows the tendancy to drag the workpiece into the cutter.
Special Fixture
Conventional milling needs special fixture (intrinsic work holding device) to hold workpiece against pulling force of cutter. However, in climb milling, it is the cutter pushing the workpiece towards the workbench, so there is no need of special fixture to hold against the force acting by the cutter.
Force
Conventional milling requires higher force whereas climb milling requires relatively lesser force when compared to conventional milling.
Friction
In conventional milling, there is massive friction between the cutter and workpiece which result in generation of large amounts of heat. However, in down milling (climb milling) there is less friction involved between the cutter and the workpiece as both.
Tool life
Conventional milling tools wear faster than those of climb milling
Tool deflection
Tool deflection during conventional milling will tend to be parallel to the cut whereas, tool deflection during climb milling will tend to be perpendicular to the cut, so it may increase or decrease the width of cut and affect accuracy.
The tooth
During conventional milling, the tooth meets the workpiece at the bottom of the cut while during climb milling; the tooth meets the workpiece at the top of the cut.
Also Read: Difference Between Shaper And Planer
Differences Between Conventional And Climb Milling
Points Of Difference | Conventional Milling | Climb Milling |
Chip Thickness | The chip width is zero at the entrance of cutting tooth and increases as the cutter finishes slicing, a factor which causes more heat to diffuse into the workpiece producing work hardening. | Climb milling on the other hand, chip width is maximum at the entrance of cutting tooth and decreases at tooth exit, so heat generated will more likely transfer to the chip. |
Also known as | Conventional milling is also known as Up Milling. | Climb Milling also known as Down Milling. |
Milling Cutter Rotation | Milling cutter rotates against the direction of feed of workpiece. | Milling cutter rotates in the same direction of feed of workpiece. |
Cutting Force | Less tool deflection is encountered but more fixturing is needed (cutting force is directed away from the workpiece. | More tool deflection is encountered but less fixturing needed (cutting force is directed onto the workpiece. |
Cutting Process | The cutting process leaves chips ahead of the cutter. It is carried upward by the tool. | The cutting process leaves chips behind the cutter. It is carried by the tool. |
Surface Finish | Surface finish in conventional milling is poor when compared to climb milling. It is generally used for the rough surface cutting operation. | Due to good surface finishing, climb milling is used for finishing operation. |
Tendency | Has no tendency to drag workpiece towards the cutter. | Shows the tendancy to drag the workpiece into the cutter. |
Special Fixture | Needs special fixture (intrinsic work holding device) to hold workpiece against pulling force of cutter. | It is the cutter pushing the workpiece towards the workbench, so there is no need of special fixture to hold against the force acting by the cutter. |
Force | Milling requires higher force. | Milling requires relatively lesser force |
Friction | There is massive friction between the cutter and workpiece which result in generation of large amounts of heat. | There is less friction involved between the cutter and the workpiece as both. |
Tool life | Conventional milling tool wear faster. | Climb milling tool tend to last long. |
Tool Deflection | Tool deflection during conventional milling will tend to be parallel to the cut. | Tool deflection during climb milling will tend to be perpendicular to the cut, so it may increase or decrease the width of cut and affect accuracy. |
Tooth | During conventional milling, the tooth meets the workpiece at the bottom of the cut. | During climb milling; the tooth meets the workpiece at the top of the cut. |
Summary
Also Read: Difference Between Orthogonal (2D Cutting) And Oblique-Cutting (3D Cutting)
The main difference between Convention Milling and Climb milling is basically the direction in which the cutter rotates. In convention milling, the cutter rotates in the anti-clockwise direction while the direction of the feed is from right to left. In climb milling, the cutter rotates in the same direction as that of the feed.